Each stage is important to ensure aviation safety during an overhaul. Checking parts for defects and cracks is one of them. Engine manufacturers have strict requirements for non-destructive testing of engine elements. Thus, only certified companies are able to carry out such procedures.
Our workshop is equipped with the necessary high-precision hardware to carry out several types of non-destructive testing:
- Magnetic particle inspection (MPI)
- Fluorescent penetrant inspection (FPI).
Magnetic particle inspection
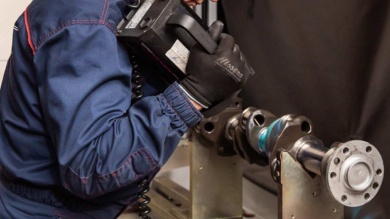
This medot allows detecting microdamages and cracks on the surface of iron, nickel, cobalt and their alloys parts at the initial stage, when they are invisible to the naked eye. However, it is these defects that make it impossible to operate the unit and require its replacement.
The control is carried out on a technical installation — a magnetic crack detector. The unit is installed and pre-magnetized and then it is covered with a special suspension, which is concentrated precisely in the places of defects and allows detecting microcracks with a depth of 0.01 mm.
Fluorescent penetrant inspection
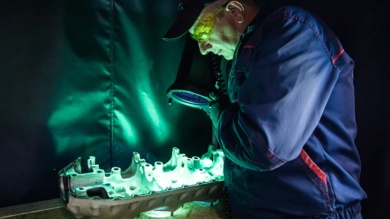
Makes it possible to reveal defects and microcracks on the surface of parts made of non-ferromagnetic materials due to an artificial increase in the light and color contrast of the defective area relative to the intact one.
Firstly, a special indicator substance (penetrant) is applied to the part, which penetrates into surface cracks and defects. Next, a developer is applied, which contributes to the defects emergence that can be seen under an ultraviolet lamp.